Seems I’ve finally got it scanned, and since I’ve wasted a lot of time in the process, wasting some more won’t really make much difference. Hope nobody gets insulted and me banned for good…
Instead of an epigraph:
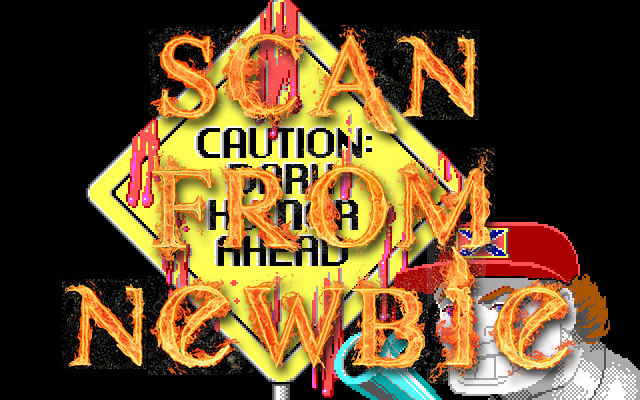
So, if you are a newbie, what do you need to make a scan of quadrocopter arm? Revopoing Mini, 10-12 hours of free time to bloody sacrifice it, RevoScan, Cloud Compare, 3dsmax/Blender and a PC to run that all on. I would prefer to have Revopoint tracking programmer at hand, also for some bloody sacrifice - even if it won’t help much, at least it might cheer me up - but alas…
Finally understanding, that software is not really my friend, but in most cases quite contrary, I am were to struggle it till I’ll gonna overcome it - even I’m not cleverer, at least I am more stubborn. So:
- Adding one pair of markers in addition to those I have on that arm already;
- Setting the arm on the platform so the complex shaped part of the detail is in the center of it (second group of scans with another end of the arm set in the middle);
- Getting Mini scanner in it’s place about 16 cm from the detail (diagonally) and tilted roughly 45 degrees down;
- Setting brightness to 3 and mode to Marker;
- Speed of the turntable was set the way it make a full revolution in about 40 seconds (360 scanning frames). It was just set that way - not because it is optimal, just it happened so;
- Also I’ve added some 6 mm 3d-printed boxes. Don’t really think they are needed in the marking mode, but just in case. By the way, sometimes the scanner thought they were markers even they are square, and not round:
Have a thought that they could affect the tracking in negative way, but only tests can find it out.
The set looks like this:
So pushing the Start button… By the way, I really recommend using theese kind of yellow glasses, when working with the scanner, since it eliminates that freaking blue flashing almost completely:
Even maybe it is not that bad to one’s eyes, it is really annoying. Especially due to the fact you can’t turn depth camera off, when RevoScan is open, and you need a few tweaks/rearrangements before next scan. Would recommend Revopoint to add this function.
This way I’ve made 9 scans: 4 sides for each end and 1 to control the final “stitching” process with tha arm centered by the middle of it. In fact I’ve used only 6 of them - 3 for each side and discarding the “intermediate” one.
Considering current scanning processs, there was nothing interesting, just a lot of time scanning and cleaning the scans after.
By the way, why I keep blaming the software… This is a Marker Mode. So when the markers are static, clear, clean, white, black, obvious and plain. And still I keep getting this after the one table round of scanning process:
Overall image is clear, there is a marker to the left, and to the right down there you can see that marker from the “left view”, I mean when it must be completely planar, but it has about 400 micron thickness, that is a bit excessive I think. Maybe it is due to those cubes, will check that, but for now I doubt they are the case. And with this Revopoint Mini was able to scan that engine part (or whatever it was), really? Maybe it was that AESUB spray, that, considering it’s price, must contain a good ammount of black magic in it, - rumors says it does, when you try to coat a copper coin with it - though I doubt it too.
At first I’ve tried to align them using multiple point alignment in CloudCompare like this:
But the results were bad as you can see in the first post of mine up there, obviousely I didn’t get “make ends meet” out of those scans.
Interestingly, the problem still may be in the fact, that I’ve used black dots, which I hoped will help tracking process in the Feature Mode, but found out they don’t help at all. And using them to aling the model, since they are visible in the point cloud, might be a bad idea. I’ll show why a bit later.
So the alignment was done completely manually in the 3dsmax. Don’t ask, how much time did I waste. Maybe I should rescan it in color mode as PUTV said up there, removing those dots first and adding new ones of different color, but I just moved the hard way since work was already done, and I didn’t want to start over again.
Considering final cleaning and alignment, I can tell you only there was a moment, when I looked upon the detail, it looked upon me, then I say “Have I finally did it?!” with it answering “Freaking yes!” in some kind of bad voice (yup, I stole that joke). And that’s all I remember.
Here you can see the final alignment with different scans in different colors:
One thing to note though. You can see that black dots I’ve made, trying to persuade the software to use it as a tracking, are visible to it not as color things or holes, but as bumps, though it was just a gel pen with overall zero thickness. And you can see to the right of the image, that on different scans they appears at different positions even they are completely static. Maybe that was the reason that multi point alignment didn’t work good, but this is a case to check in future scans.
The final mesh looks this:
Some quiet perfectionalist voice said “Hey, there is some obvious misalignment on one of the sides” following me and the detail itself bellowing “To hell with it!” in the same time.
BTW would recommend to add in the “Isolation” section of the RevoStudio “Keep markers” button, so the central parts of the markers won’t be deleted by using it. Though unsure is it easy to implement or not - markers produce obvious 5 mm diameter flat point cloud patches, but does it really help or not to make this, unsure.
Final thoughts: it seems the turntable produces some vibration due to either gears used or using of stepper motors with not enough substep division (didn’t disassemble to look closely), so it may produce some bad influence on the scanning process (one of the tracking object I’ve added began to vibrate, so I’ve removed it) and there is some turning speed, that is the best one, that may reduce vibration and having good enough exposure at the same time, but I can’t effectively test it. Yeah, PUTV has mentioned it,but I can’t neither find, nor want to test.
Secondly, gonna buy some zinc oxide to try to coat the detail scanned with it using airbrush, hope it won’t get clogged, since the AESUB due ot it’s price and availability is not really an option, but it might or might not be a different story. And thank you, those, who read it to this point and manged not to get asleep. Cheers.